
On the production of iron ore superconcentrates by high
1975.6.1 On the production of iron ore super- concentrates by high-intensity wet magnetic separation. Int. J. Miner. Process., 2: 117--126. Direct reduction of iron ore to produce electric furnace feed for steelmaking is be- coming economically important on a
Charlar en Línea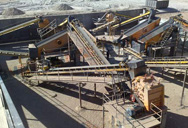
Wet magnetic separation of Siberian iron-ore concentrates
2014.5.27 Wet separation of the primary Siberian iron-ore concentrates processed at Abagursk enrichment facility (OAO Evrazruda) is studied in the laboratory. Nine samples
Charlar en Línea
Developments in the physical separation of iron ore: magnetic ...
2015.1.1 The ore is mainly composed of magnetite, hematite, martite, and quartz. It is very difficult to produce a high-quality iron ore concentrate by magnetic separation alone
Charlar en Línea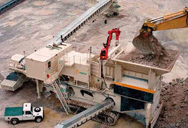
Model of Stabilization of the Quality of Iron-Ore Concentrate
2018.8.20 In the present paper, we reflect the main aim of control over the process of separation of iron ore in the course of wet magnetic dressing. We propose a pr Model of
Charlar en Línea
Wet low intensity magnetic separators - Metso
2018.8.29 General Metso has produced several thousand Low In-tensity magnetic separators (LIMS) both dry and wet versions to the iron ore industry.
Charlar en Línea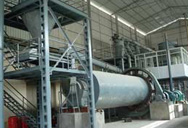
Comminution and classification technologies of iron ore
2022.1.1 Abstract Hematite and magnetite, the two predominant iron ores, require different processing routes. High-grade hematite direct shipping ores generally only
Charlar en Línea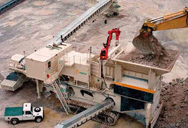
Wet High Intensity Magnetic Separation of Iron
1996.1.1 In this study, the impurities removal process for low-grade Sanje iron ore was developed using Wet High-intensity magnetic separation (WHIMS) and Reverse flotation (RF).
Charlar en Línea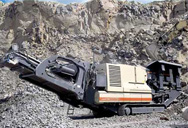
Influence of Magnetite Grain Size on Magnetic
2023.7.5 Wet magnetic separation is the main beneficiation process at iron ore enterprises in Russia and abroad. Conventional magnetite ore processing flowcharts exclude tailings from the process after each
Charlar en Línea
Wet Magnetic Separation of Siberian IronOre
2017.8.28 Table 1 presents the characteristics of wet magnetic separation of the primary concentrates and the results of chemical analysis of the separation products.
Charlar en Línea
DESULFURIZATION OF IRON ORE CONCENTRATE USING
2021.7.29 concentrate. The magnetic concentrate is produced by crushing, comminution and Low-Intensity Magnetic Separation (LIMS). Approximately 70 % of the
Charlar en Línea
(PDF) Low-Intensity Magnetic Separation: Principal
2004.6.1 Characteristics of the mineral phases in the feed into a wet magnetic separation 2. ... More recently, mo st iron-ore beneficiation plants employed ... Magnetic concentrate. Classification. Deslim ...
Charlar en Línea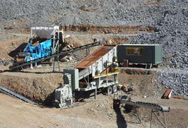
(PDF) Dry Permanent Magnetic Separator: Present
2022.9.30 iron ore resources, a dry, low-cost p rocessing or pre-sorting prior to the wet separation has received the attention of industrial practitioners as a potential alternative. The performance of dry ...
Charlar en Línea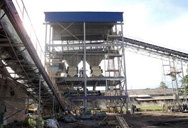
Magnetic separation studies for a low grade siliceous iron ore sample ...
2013.1.31 The best concentrate with 92,47% Fe2O3 grade and 69,91% recovery yield could have been obtained from the ore containing 62,94% Fe2O3 by high intensity wet magnetic separation method at 6000 Gauss ...
Charlar en Línea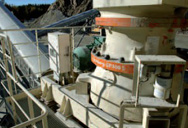
(PDF) Recovery of magnetite from dry crushed feed using wet
2019.9.29 The aim of this study is to examine the performance of wet drum magnetic separation on the recovery of magnetite from dry crushed feed. The steel industry has depended on iron (Fe) concentrate ...
Charlar en Línea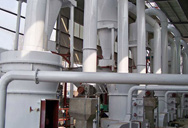
The mechanism of magnetics capture in the wet drum magnetic
2000.3.1 Magnetic separation is a versatile technique widely used in the mining industry. Drum-type wet low-intensity magnetic separation (WLIMS) represents the backbone of the iron ore upgrading circuits since the mid 19 th century. However, it has been traditionally applied through guidelines that commonly disregard the ore properties
Charlar en Línea
A New Route to Upgrading the High-Phosphorus Oolitic Hematite Ore
2022.4.30 The roasted briquettes were subjected to wet magnetic separation under conditions of grinding fineness of 80% less than 0.045 mm and magnetic field intensity of 1200 Gs, and the rough magnetic separation concentrate contained 57.49% Fe and 1.4% P 2 O 5, with an iron recovery rate of 87.5% and a dephosphorization rate of 34.27%.
Charlar en Línea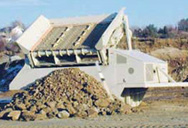
6 Magnetic Separation - Springer
2017.8.25 separators are usually the last stage of magnetic separation to make a final magnetic concentrate and a nonmagnetic tailing. Dry Magnetic Separators (i) Magnetic head-pulley separators are the most common types of dry unit, and can be used both for magnetic particle concentration and tramp iron removal. The Trajectory of magnetic
Charlar en Línea
(PDF) An overview of the beneficiation of iron ores via
2014.3.1 Prasad et al. (1988) have studied iron ore slimes processed by magnetic separation at the Kiriburu mines in India. A c oncentrate containing 63% Fe and 3.3% Al 2 O 3 with an iron recovery of
Charlar en Línea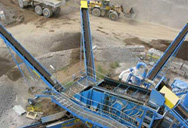
Effect of frictional grinding on ore characteristics and
2018.6.15 Frictional grinding was evaluated to improve the selectivity of two magnetite samples A and B in the magnetic separation process. Sample A containing 64.42% Fe was a magnetite concentrate upgraded from a low grade magnetite Ore, Sample B, containing 46.63% Fe, through an upgrading process involving 1-stage ball milling and
Charlar en Línea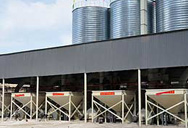
Assessing the performance of a novel pneumatic magnetic separator for ...
2020.9.1 Dwari et al. (2013) used a combination of dry and wet magnetic separation methods to upgrade a low-grade siliceous iron ore with magnetite, hematite, and goethite as major iron minerals. The study showed that for particles finer than 200 µm, the separation methods produced a magnetic concentrate with 67% iron and iron recovery of 90%.
Charlar en Línea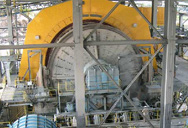
Minerals Free Full-Text Economic and Socio
2020.10.26 In our previous studies, we demonstrated the performance of novel superfine crusher and pneumatic planar magnetic separator as energy-efficient technologies for dry processing of magnetite ores. The present study investigates the economic and socio-environmental benefits of applying these technologies in conceptual dry magnetite
Charlar en Línea
(PDF) Increasing the efficiency of iron-ore dressing by separation
2021.5.31 Osipova N. V. Automatic control system for wet magnetic separation of iron ore. Gornyi Zhurnal. ... using roasting-magnetic and regrinding-magnetic separation, the iron concentrate with iron grade ...
Charlar en Línea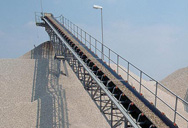
ENRICHMENT OF LOW GRADE MAGNETITE ORE BY MAGNETIC
2021.1.8 In the second option, the iron ore tail is treated in a similar approach, but the gravity concentration replaced by magnetic separation results in a product quality with 65.34% Fe, 3.70% SiO2 and ...
Charlar en Línea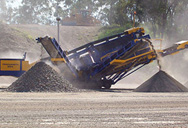
International Journal of Engineering
2023.8.3 the iron ore grade by magnetic methods in recent years, as mentioned below. Shao et al. [21] investigated the processing of Esmalon iron ore by magnetic separation method. They obtained a 63% iron grade concentrate and a 65% recovery rate by a low-intensity wet magnetic separator.
Charlar en Línea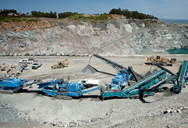
Improved iron recovery from low-grade iron ore by efficient
2022.8.1 At this time, iron minerals could be effectively recovered by a grinding and low-intensity magnetic separation process. Under the optimum roasting and magnetic separation conditions, the iron grade of magnetic concentrate reached 66.40 %, the iron recovery was 92.44 %, and the sulfur content decreased significantly from 0.547 % to
Charlar en Línea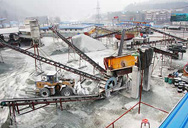
Influence of Magnetite Grain Size on Magnetic
2023.7.6 Keywords: Magnetite, magnetite concentrate, magnetic susceptibility, sieving, sieve residue, magnetic separation. DOI: 10.1134/S1062739123010155 INTRODUCTION Wet magnetic separation is the main beneficiation process at iron ore enterprises in Russia and abroad. Conventional magnetite ore processing flowcharts
Charlar en Línea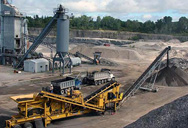
Wet magnetic separation of Siberian iron-ore concentrates
2014.5.27 Wet separation of the primary Siberian iron-ore concentrates processed at Abagursk enrichment facility (OAO Evrazruda) is studied in the laboratory. Nine samples of concentrates (−0.07 mm class) from magnetite ore and weakly oxidized ore are subjected to wet magnetic analysis in a field of 80 kA/m. The basic magnetic characteristics of the
Charlar en Línea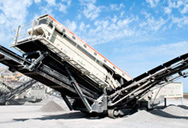
Minerals Free Full-Text Economic and Socio-Environmental Benefits ...
2020.10.26 In our previous studies, we demonstrated the performance of novel superfine crusher and pneumatic planar magnetic separator as energy-efficient technologies for dry processing of magnetite ores. The present study investigates the economic and socio-environmental benefits of applying these technologies in conceptual dry magnetite
Charlar en Línea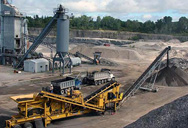
Iron ore after magnetic separation: (a) tailings; (b) iron-ore ...
Fig. 5 shows the iron ore after the process of magnetic separation. The concentrate (b) has a pronounced dark color due to the iron oxides in its composition while the tailings (shown by clastic ...
Charlar en Línea