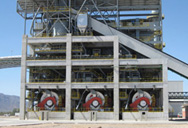
Effect of Adding Limestone on the Metallurgical
2021.1.14 One of the most common fluxing materials for iron ore pellet production is limestone, which is mainly calcium oxide (CaO). In this study, the effect of adding
Charlar en Línea
Effect of adding limestone on the metallurgical properties of iron ore ...
2015.8.10 One of the most common fluxing materials for iron ore pellet production is limestone, which is mainly calcium oxide (CaO). In this study, the effect of adding
Charlar en Línea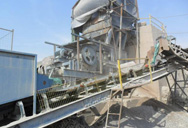
(PDF) Iron Ore Pelletizing Process: An Overview
2018.7.11 1 Certain sub- stances such as hydrated lime serve as both additive and binder. Fines of anthracite or coke are also added
Charlar en Línea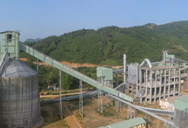
Iron Ore Pelletizing Process: An Overview
2018.7.11 This chapter aims to provide an overview and the evolution of iron ore pelletizing process including: Pelletizing process and raw
Charlar en Línea
Effect of limestone and dolomite flux on the quality of
2021.2.1 In addition to that, the presence of CaO and MgO content played a significant role in the preparation of iron ore fluxed pellet attaining basicity of 0.43–0.64
Charlar en Línea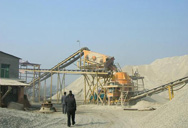
Effect of Adding Limestone on the Metallurgical Properties of Iron Ore ...
2015.6.5 Limestone fluxed iron ore pellets are reduced in CO-rich atmosphere generally accompanied by swelling behavior.
Charlar en Línea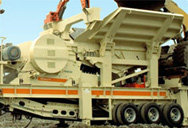
Iron Ore Pelletizing Process: An Overview - IntechOpen
2018.7.17 The iron ore pelletizing process consists of three main steps: Pelletizing feed preparation and mixing: the raw material (iron ore concentrate, additives
Charlar en Línea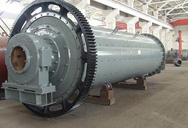
Influence of flux additives on iron ore oxidized pellets
2010.8.5 Abstract Six additives, i.e., limestone, lime, magnesite, magnesia, dolomite and light-burned-dolomite, were added for investigating their influences on the pellet
Charlar en Línea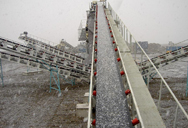
Effect of limestone and dolomite flux on the quality of
2020.10.23 DOI: 10.1016/j.powtec.2020.10.063 Corpus ID: 226333476; Effect of limestone and dolomite flux on the quality of pellets using high LOI iron ore
Charlar en Línea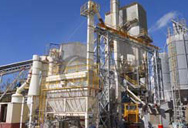
Iron Ore Pelletizing Process: An Overview - IntechOpen
2018.7.17 The iron ore pelletizing process consists of three main steps: 1. Pelletizing feed preparation and mixing: the raw material (iron ore concentrate, additives anthracite, dolomite and binders are prepared in terms of particle size and chemical specifications, dosed, and mixed together to feed the pelletizing process; 2.
Charlar en Línea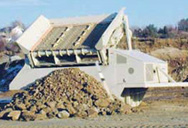
Influence of flux additives on iron ore oxidized pellets
2010.8.5 Six additives, i.e., limestone, lime, magnesite, magnesia, dolomite and light-burned-dolomite, were added for investigating their influences on the pellet quality. For green balls, adding lime and light-burned-dolomite makes the wet drop strength decrease firstly, and then increase with further increase of additive dosage. Ca(OH)2 affects the
Charlar en Línea
Ore Sinter - an overview ScienceDirect Topics
Pelletizing involves the forming of ore fines (pellet feed) and concentrates with grain sizes of well under 1 mm into pellets of around 10 to 15 mm in diameter by addition of a binding agent. The pellets are first formed in rotating drums or on rotary discs and thereafter dried and indurated at temperatures above 1273 K.
Charlar en Línea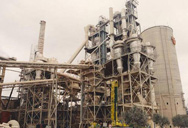
Metals Free Full-Text Influence of Basicity and Calcium
2022.6.20 The application of fluxed pellets in iron making industry has attracted considerable attention because of the better metallurgical properties than acid pellets and environmental friendliness compared to sinters. However, fluxed pellets with different binary basicity (CaO/SiO2) exhibited significant differences in phase composition,
Charlar en Línea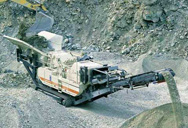
Iron Ore Pelletization: Part I. Fundamentals Request PDF
2021.3.15 The binder is an important additive widely applied in pelletizing iron ore concentrates, making iron ore pellets available as feedstocks for blast furnace ironmaking or direct reduction processes ...
Charlar en Línea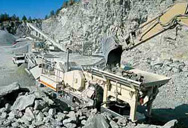
Iron ore pelletization - ScienceDirect
2015.1.1 The ratio in the output from the three main pelletizing technologies changes depending on practical circumstances, such as iron ore reserves, iron ore types, market demand, and required investment. The ratio for grate-kiln pellets has increased to 55.33% in 2011 from 7.21% in 2000, while the ratio for shaft furnace pellets has dropped to 42.05% ...
Charlar en Línea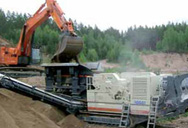
Investigation on Loss on Ignition to Study the Effect of Iron Ore ...
2021.10.24 This study corroborates that the iron ore mineralogy has significant effects on green pellet growth and its properties by both experimental and mathematical arguments. In this context, three iron ore samples with different loss on ignition (LOI): 2.64, 4.85 and 9.19 wt.% were taken. The mineralogical differences were investigated through
Charlar en Línea
(PDF) Iron Ore Sintering: Process - ResearchGate
2017.2.16 Sintering is a thermal agglomeration process that is applied to a mixture of iron ore fines, recycled ironmaking products, fluxes, slag-forming agents and solid fuel (coke). The purpose of the ...
Charlar en Línea
Role of Ferrous Raw Materials in the Energy Efficiency of
The Nordic ferrous burdens consist of almost 100% pellets plus briquettes and trim additives. 4) The elimination of sintering resulted in a net gain in energy efficiency in the chain from mine to steel which we have described in an earlier work. 5) In addition, the dominant source of iron ore for pelletizing and sintering is very high grade.
Charlar en Línea
Effect of Limestone and Dolomite Flux on the Quality of
2020.10.23 The effect of lime addition in hematite iron ore pellets on its physico-chemical as well as mechanical properties with respect to blast furnace requirement was studied in a laboratory scale with ...
Charlar en Línea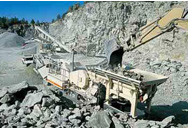
Influence of Pellet Basicity (CaO/SiO 2 ) on Iron Ore Pellet
The limestone addition, i.e. basicity–CaO/SiO 2 of pellet decides the mode, temperature and the amount of melt formed. The properties of the pellets are, therefore, largely governed by the form and degree of bonding achieved between ore particles and also by the stability of these bonding phases during the reduction of iron oxides.
Charlar en Línea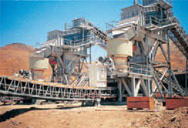
Iron ore fluxed pellets and their physical properties
1985.6.1 The moisture content of iron ore fluxed pellets was calculated proportionally according to the amount of water required by pure iron ore and pure limestone pellets (13.5% and 16.5% respectively). Therefore, a fluxed charge containing 10% limestone needs 13.8% water and a charge containing 20% limestone needs 14.1% water content.
Charlar en Línea
Iron ore sintering - ScienceDirect
2022.1.1 In addition, decrepitation of iron ore particles affects the physical stability of granules and consequently the permeability of the sintering bed. ... In contrast to the conventional sintering process, the blended ore, limestone, and burnt lime are first mixed and pelletized in the HPS process using disk pelletizers to produce green pellets ...
Charlar en Línea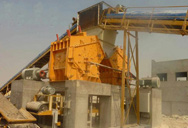
Iron Ore Pelletization: Part II. Inorganic Binders Request PDF
2021.7.5 The binder is an important additive widely applied in pelletizing iron ore concentrates, making iron ore pellets available as feedstocks for blast furnace ironmaking or direct reduction processes ...
Charlar en Línea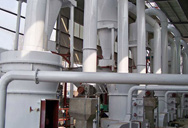
(PDF) Iron Ore Sintering: Raw Materials and Granulation
2016.10.28 Abstract and Figures. Sintering is an agglomeration process that fuses iron ore fines, fluxes, recycled products, slag-forming elements and coke. The purpose of sintering is to obtain a product ...
Charlar en Línea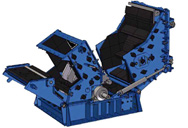
Effect of limestone and dolomite flux on the quality of
2020.10.23 DOI: 10.1016/j.powtec.2020.10.063 Corpus ID: 226333476; Effect of limestone and dolomite flux on the quality of pellets using high LOI iron ore @article{Prusti2020EffectOL, title={Effect of limestone and dolomite flux on the quality of pellets using high LOI iron ore}, author={Pallishree Prusti and Kashinath Barik and Nilima
Charlar en Línea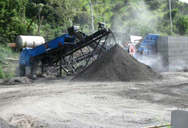
(PDF) EVOLUTION AND GROWTH OF IRON ORE PELLETIZING
2022.6.16 In the last years, pelletizing has been playing an important role for iron ore mining and ironmaking. Some factors have contributed to this fact like as: depletion of high-grade iron ore reserves ...
Charlar en Línea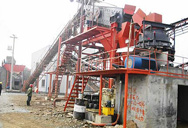
(PDF) Green Ironmaking Industry: Production of Iron
2023.5.2 Chemical compositions of the iron ore, dolomite, and lime sludge used as inputs for producing iron-ore pellets. Component (wt%) Iron ore Coal ash Bentonite Dolomite Lime sludge Al 2 O 3 0.73 26.81 ...
Charlar en Línea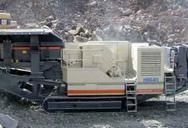
(PDF) Influence of Pellet Basicity (CaO/SiO2) on Iron Ore
The chemical analysis of the raw material is shown in the Table 1. Iron ore fines and lime- stone of 10 mm size were ground separately in laboratory ball mill. Green pellet mix was prepared by mixing the iron ore fines, limestone, bentonite and Corex sludge as per Table 2. Green pellets were prepared using laboratory scale balling disc.
Charlar en Línea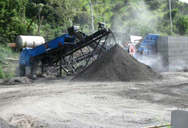
The effect of particle size on green pellet properties of iron ore
2017.1.1 Direct reduction (DR) of iron ore with hydrogen is a potential route for near-zero CO2 steelmaking, but vertical shaft DR reactors require that iron ore fines must first be pelletized.
Charlar en Línea