
(PDF) Cold briquetting of iron ore fines for DRI
2019.7.22 The present work describes the possibility of cold-briquetting of fine iron ore to produce DRI (Direct Reduced IRON) in
Charlar en Línea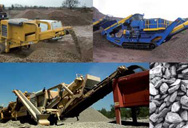
Cold Briquetting of DRI Fines for Use in Steel Making
2020.2.26 Usually, briquetting is done with iron ore, fluxes, coal and process wastes. In the present study, DRI fines are the major component. Hence, the briquetting is done
Charlar en Línea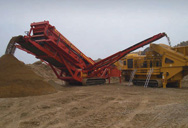
Cold briquetting of iron ore fines for DRI production:
RECYRON is a highly flexible process to utilize fine ore as well as all possible iron ore and carbon containing wastes to produce DRI. A comparative description of these three
Charlar en Línea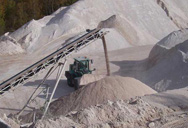
Briquetting of Fine‐Grained Residues from Iron and Steel
2020.7.7 The aim is to collect the fines, dusts, and sludge generated in the Midrex process, briquetted it, and charged the briquettes directly back to the shaft together with
Charlar en Línea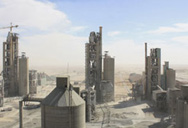
Finite element analysis of briquetting of iron ore fines
2019.7.15 Our work can be help optimise the briquettes process of iron ore fines. In this work, a numerical model of briquetting process has been conducted to analyse the
Charlar en Línea
IOP Conference Series: Materials Science and
In the present study, briquettes are made by a stiff extrusion process from metallurgical waste like iron ore fines and coke fines with the addition of Portland cement as a binder
Charlar en Línea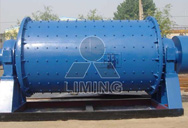
Finite element analysis of briquetting of iron ore fines
2019.7.15 The briquetting behaviour of iron ore fines was investigated using the Finite Element Method (FEM). The Drucker-Prager Cap (DPC) model was utilized and the
Charlar en Línea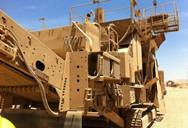
Direct Reduced Iron By-Product Fines (DRI D): A Guide
2021.6.22 Reduced Iron Fines has been designated as Direct Reduced Iron (D) (By-product Fines with moisture content of at least 2%), abbreviated hereinafter to DRI (D).
Charlar en Línea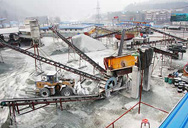
Briquetting of Fine-Grained Residues from Iron and Steel
2020.12.17 1. Introduction on briquette strength. As briquettes are characterized by high density and low porosity, they have a worse reducibility compared During the
Charlar en Línea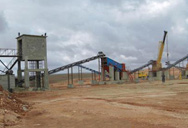
Finite element analysis of briquetting of iron ore fines
2019.7.15 Fig. 2 a shows the briquetting system simulated in the study. The true density of iron ore fines (mainly goethite and hematite) was 4314 kg/m 3, and the initial bulk density of the compact was 1952 kg/m 3, giving the initial relative density of the powder bed 0.45.The roll speed was 10 rpm and the feeding pressure was 2 MPa.
Charlar en Línea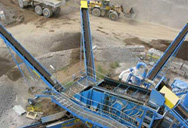
Use of Bentonite and Organic Binders in the Briquetting of
2021.8.5 The reducing gas hydrogen, the inert gas argon, and the inert gas nitrogen were purchased from Nippon Gases. Iron ore pellets, which were delivered by voestalpine Stahl GmbH, were used as a reference in the reduction tests. These iron ore pellets had a mean iron content of 66.1 wt%, with the iron being in the form of Fe 2 O 3. The grain size
Charlar en Línea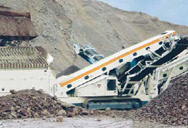
Cold Briquetting of DRI Fines for Use in Steel Making Process
2019.12.7 DRI fines, generated during its manufacture and handling, generate high content of fines in the size fraction less than 2 mm. It has iron content above 80%. It is difficult to directly use such iron-rich material in the primary steel making process, without agglomeration. At JSW Steel Vijayanagar, around 50 to 70 tons per day of DRI fines with
Charlar en Línea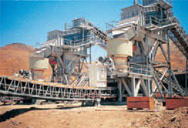
Processing and Characterization of Self-Reducing Briquettes
2021.9.13 The powder was roasted in a muffle furnace at 950 °C for 60 min to remove hydroxide species and impurities. Most of the jarosite species decomposed into hematite, increasing the iron oxides concentration from 33 to 55 wt%, and reducing considerably the S content from 8.86 to 2.55 wt%, decomposed in the form of SO x gas
Charlar en Línea
Modeling and Experimental Study of Ore-Carbon
2018.3.23 Iron ore-carbon briquette is often used as the feed material in the production of sponge iron via coal-based direct reduction processes. In this article, an experimental and simulation study on the reduction behavior of a briquette that is made by hematite and devolatilized biochar fines under CO–CO2 atmosphere was carried out.
Charlar en Línea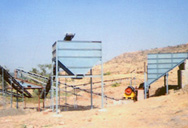
Iron ore briquettes, lump, biomass DRI may ease steel
2023.5.5 Hot DRI charged into an EAF typically generates the most efficiency, compared with briquetting and heating cold charge. FerroSilva expects its process to require less than a tenth of the electricity per ton of iron compared with electrolysis-based green hydrogen plants, and can generate byproducts such as liquid biogenic CO2.
Charlar en Línea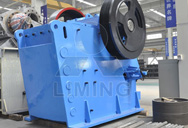
Study of an Organic Binder of Cold-Bonded Briquettes with
2.1.1. Iron Ore Raw Material . Two types of iron bearing materials in this work came from Gansu Province, China, and they were labelled as samples A and B. Sample A is return fines of sinter generated in the sintering process; sample B is iron ore fines containing titanium, which could decrease the cost of protecting blast furnace lining.
Charlar en Línea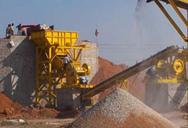
Cold-Briquetted Iron and Carbon (CBIC), investigation of
2020.5.1 Cold-Briquetted Iron and Carbon (CBIC) is an innovative, patented product that is obtained from cold briquetting process of CDRI (Patent No. IR60923). Thanks to this technology, direct reduction plants producing CDRI which cannot use their full production capacity due to the insufficient customers nearby, ...
Charlar en Línea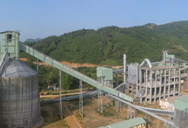
Briquetting of Fine‐Grained Residues from Iron and Steel
2020.7.7 4 Briquetting with a Binder. Cold bond briquetting may offer a method for recycling the residues. Fines, dusts, and sludge can be briquetted using a binder to a form that is suitable for charging into the Midrex shaft. To get briquettes with sufficient mechanical strength and thermal stability, a binder is needed.
Charlar en Línea
(PDF) Effects of Binder on the Properties of Iron Ore
2010.4.1 Iron ore-coal composite pellets were prepared by cold bonding. Various binders such as lime, Ca (OH)2, slaked lime, dextrose, molasses, and sodium polyacrylate (SPA), alone or in combination, were ...
Charlar en Línea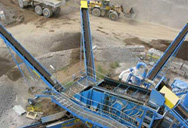
Maximizing the Recycling of Iron Ore Pellets Fines Using
2023.5.22 This research work focuses on the practicality of using organic binders for the briquetting of pellet fines. The developed briquettes were evaluated in terms of mechanical strength and reduction behavior with hydrogen. A hydraulic compression testing machine and thermogravimetric analysis were incorporated into this work to investigate
Charlar en Línea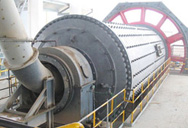
Reduction of Iron Ore Fines using "SYNGAS" from Lean- Grade
2016.11.28 Iron ore fines are subjected to sieve analysis to get different sizes of ore particles. Particles in the range of 63 µm to 250 µm size have been used for briquetting. 4 % bentonite, 4 % molasses ...
Charlar en Línea
Development of Cold-Bonded Briquettes Using By-Product
2022.2.18 The briquetting process has several benefits including energy savings and reducing environmental load and costs ... Lampinen H, Eriksson L (1999) Recycling of in-plant fines as cold-bonded agglomerates. Belgium, Brussels. ... Iron ore pellets for blast furnace and direct reduction feedstocks — Determination of the crushing strength (BS
Charlar en Línea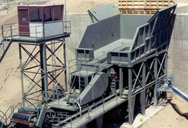
INNOVATIVE SOLUTIONS ON RECYCLING OF OXIDE
2023.5.9 The recycled by-products in this concept are fine dusts like iron ore fines or EAF dust (0-3 mm) and HBI fines (0-6 mm), pre-dried slurry fines (max. humidity 20wt% H2O) ... Cold briquetting process for reutilization in DR plants. Figure 6. Block diagram of cold briquetting process of different dusts, mill scale and dry sludge. ...
Charlar en Línea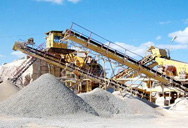
Direct Reduced Iron By-Product Fines (DRI D): A Guide
2021.6.22 iron ore burden is such that the ascending column of g ases interfaces with the maximum surface area of the iron ore - the higher the content of iron ore fines in the feedstock, the lower the permeability of the burden. The iron ore feedstock (pellets and lump ore) is therefore screened to remove fines before being charged to the furnace.
Charlar en Línea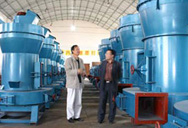
On the reduction behavior, structural and mechanical features of iron ...
2017.1.1 The iron-carbon composites were produced by cold briquetting in a Komarek B050 roll press machine using a force of 35 kN.The briquettes were produced with pillow-shape and dimensions of 39 mm length, 19 mm width and 15 mm thick.They were cured in an oven for 24 h at 35 °C (Fig. 1).The relative proportions of the components of
Charlar en Línea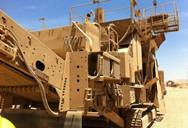
Recovery of iron rich residues from integrated steel making process
2019.10.1 This study aimed at verifying the technical feasibility of recovering and reusing several iron-rich residues from the steel production process through the production of briquettes that could potentially be reintroduced as a ferrous source into the converters during the transformation of hot metal into liquid steel. An experimental investigation was
Charlar en Línea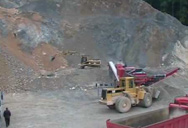
Review of briquette binders and briquetting mechanism
2018.2.1 Abstract. Briquette binder plays a key role in the process of briquette production. The quality and performance of briquette also depend on the quality of briquette binder. Different types of ...
Charlar en Línea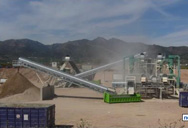
Inside Vale’s green briquette megahubs and how they will work
2023.5.11 “Vale’s green briquettes are produced with very flexible and low-carbon technology. Since it is an agglomerate from iron ore fines, the resulting direct-charge material has all the necessary attributes to be used directly in conventional, mature and existing ironmaking reactors such as blast furnaces and direct- reduction furnaces,”
Charlar en Línea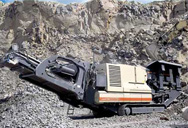
Effect of Briquetting Pressure on the Properties, Reduction
2022.12.5 Return fines of sinter were used to prepare cold-bonded briquette (CBB) with different briquetting pressure and properties, and reduction behavior and reduction kinetics of CBB were investigated in the current study. Increasing the briquetting pressure leads to the increase of the CBB’s compressive strength. The changing tendency of the
Charlar en Línea